"Surface treatment technology" refers to the process of artificially forming a surface layer with different mechanical, physical and chemical properties on the surface of the base material to meet the requirements of corrosion resistance, wear resistance, decoration or other special functions of the product. Different There are many kinds of printing materials, some materials can be printed directly without prepress treatment, such as paper, plastic, glass, etc., and the surface treatment technology of different materials is also different. This article The surface treatment methods commonly used in the printing industry are described as follows.
For PS (polystyrene) and PVC with polar structure, no surface pretreatment is required before printing, but for PP, PE, PET, etc. whose surface structure is non-polar, their chemical stability is extremely high, and it is not easy to be affected by large Most ink solvents penetrate and dissolve, and the binding fastness to ink printing is very low, so surface treatment must be carried out before printing to activate the plastic surface to generate new chemical bonds to roughen the surface, thereby improving the bonding and adhesion of the ink and the film surface. Fastness; at the same time, in the process of manufacturing some pellets, a certain amount of additives, additives, and lower opening agents are added according to different requirements. These oil layers are completely unfavorable to printing. They make the film surface difficult to bond and reduce the adhesion. Therefore, the film materials with these oil layers must undergo surface treatment to remove the grease on the surface of the film and improve the ink and coating. Adhesion fastness.
Printing surface treatment technology was first developed to solve the problem of poor adhesion of plastic film surface printing and coating. The basic materials of plastic films are mainly polypropylene (PP), polyhexene (PE), polyvinyl chloride (PVC), polyester (PET), etc. The surface characteristics of plastic films are determined by the polar groups of the molecular structure substrate, the degree of crystallinity and the degree of plasticity. There are great differences in chemical stability and other factors, and these factors have a great influence on the adhesion fastness of the printing ink layer.
-
Prepress surface treatment of paper
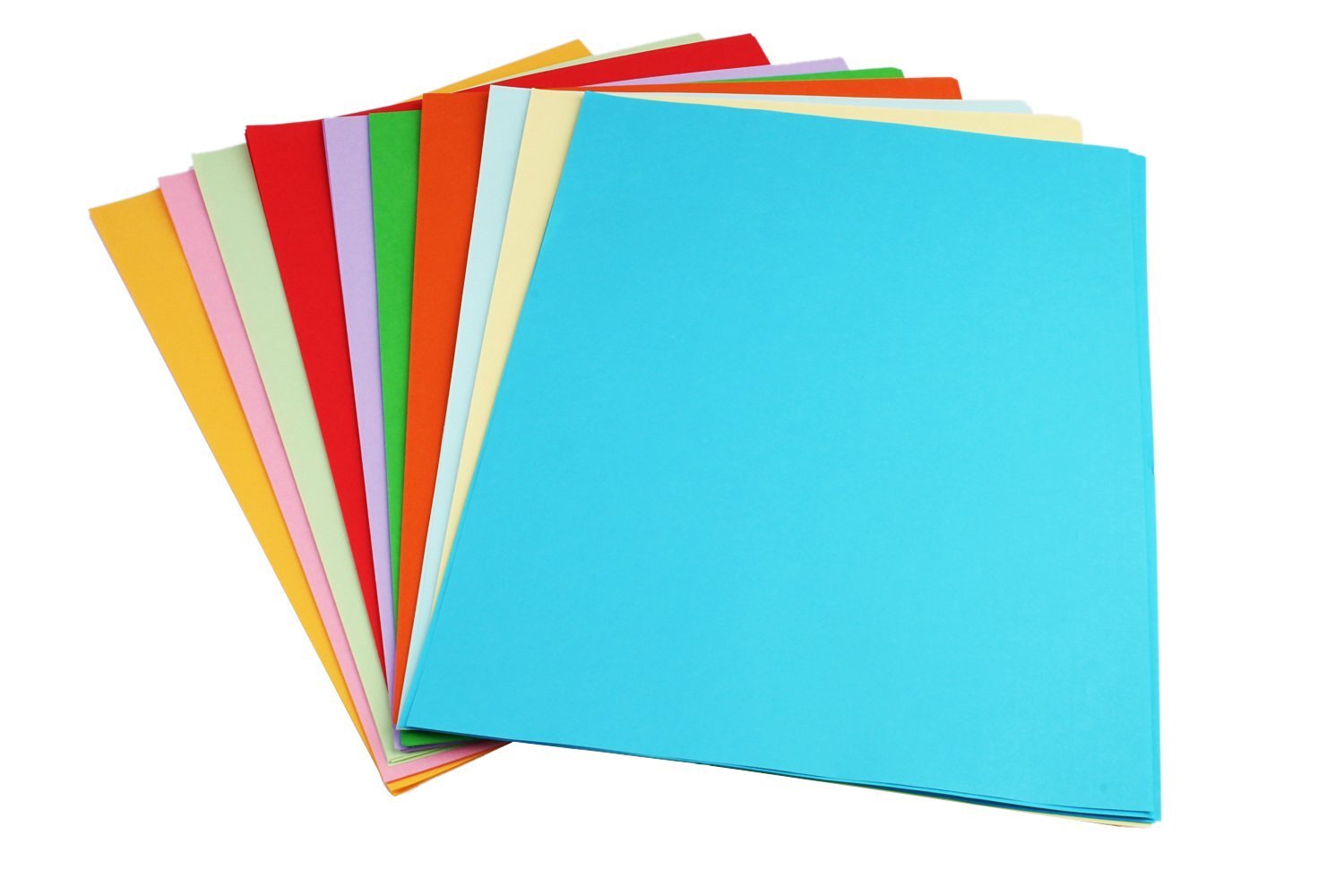
First from a commercial point of view, surface treatment is a way to provide added value to paper and cardboard products, and secondly, it can also be said to be a method to reduce the net cost of materials, in fact, from a material point of view, it is a way to add value to paper and cardboard products Provide a way to modify
Strength properties - stiffness, tensile strength, compressive strength
Optical properties—whiteness, brightness, opacity
Absorptive properties - wettability and absorbency;
Surface Properties - Roughness, smoothness and friction properties.
Humidity treatment
The deformation of paper includes force deformation and natural deformation. Natural deformation is mainly caused by water content. Since the main component of paper is cellulose, and the structural formula of cellulose contains multiple hydroxyl groups, these hydroxyl groups determine that it has a strong hydrophilic force; There are gaps between the fibers and the filler, and these pores have an adsorption effect on water. After the paper absorbs water, the fibers will expand, which will increase the size of the paper and shorten the size of the paper after high temperature dehydration, which will affect the overprinting.
If the water content of the paper is too high, the surface strength of the paper will be reduced. In light, individual fibers will be disconnected during printing, commonly known as fluffing. If the water content is too low, the paper will become hard and brittle, and the tearing degree, folding resistance and bursting resistance will be reduced, making paper feeding and delivery difficult, and overprinting difficult to be accurate. In order to make the water content of the paper uniform and suitable for the printing workshop, reduce the sensitivity of the paper to water and improve the dimensional stability, it is necessary to carry out humidity conditioning treatment before printing.
Humidity conditioning treatment is to hang the paper in the drying room under normal temperature and pressure and a certain relative humidity. After a period of time, the moisture content of the paper is balanced and adapted to the temperature and humidity of the printing workshop, which is called humidity conditioning. The methods include: isohumidity adaptation method, hygroscopic method, dehumidification method, cold water reprinting method, etc.
Coating surface treatment
Most surface treatments are applied to lay the groundwork for further coating outside the machine, especially to improve positioning control, ie: Z coverage capability and surface properties, X-Y variability. Base paper is an important factor affecting the effect of surface treatment.
The positioning "control" effect depends on the base paper itself. Proper control of base paper properties remains a challenge for surface preparation. Although surface sizing can control wettability and absorbency, it does not improve the non-uniformity during forming and the appearance of the paper. And these structural properties determine the uniformity of the paper: the surface structure deforms at the bottom of the forming.
The importance of base paper consistency is the amount of pressure applied to the final coating, which is higher for size press, roll coating, and bar or blade metered coating. It determines whether changes in coating thickness and uniformity can produce acceptable products. In the future, advanced real-time testing methods and data processing equipment will be used to record parameters such as surface distribution, formation and permeability.
Other advantages of pre-calendering are limited if pre-calendering bends the surface towards the floe structure. Although the roughness fluctuation may be reduced, calendering cannot change the roughness change in the X-Y direction and the surface is still uneven. In addition, calendering can cause local variations in paper tightness, absorbency, and surface consistency, which can affect coating structure and uniformity.
Functional coatings
Not all coatings are to be dyed, the development of adhesives, repellants and release coatings often starts in-machine with surface sizing agents (etherified or esterified starches, alginates and polyvinyl alcohols) apply. Whether it is silicon release coating, or adhesive and protective coating, the covering ability and economy of the functional coating layer are improved. Control of the covering ability of any additional layers (whether silicon or printing inks) is a critical part of the function of the coating. Protective coated paper and paperboard are versatile and can be used as food wrapping paper, paperboard, labels, roll and ream packaging, and protective paper. Most of the current research is in this direction.
-
Plastic and plastic products
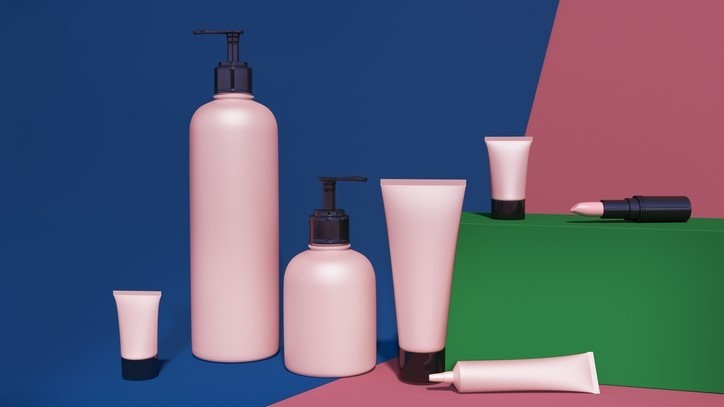
With the wide application of plastic products, the coating of plastic surfaces has been increasing day by day. After the plastic is painted, it can not only improve the weather resistance, chemical resistance, surface hardness, reduce the insulation performance, prevent adhesion and dust resistance, improve the hand feeling performance, but also improve the artistic effect of decoration, so that the plastic surface has a variety of colors. Glossy, plump, three-dimensional, etc.
Let's talk about the treatment method of plastic surface. There are many methods of plastic surface treatment. Generally, chemical treatment, solvent treatment, flame treatment, plasma treatment and corona treatment are commonly used.
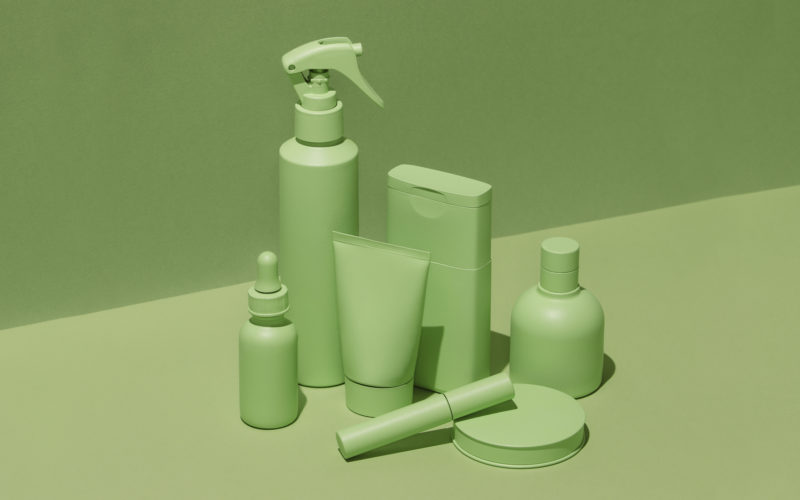
Chemical Treatment
Also called chemical oxidation. Polyethylene (LDPE), polystyrene (PS) and ABS plastics are used for oxidizing liquid treatment on the surface of plastics. The surface of the plastic film can also be coated with chemicals such as potassium permanganate chlorosulfonic acid, naphthenic chromic acid, etc., so that the surface can be chemically corroded to improve the wetting ability of the ink.
Solvent Treatment
Commonly used trichloroethylene solution, the temperature is 65~75 ℃, after etching with solvent vapor, coating quickly, the time should be within 30~60 seconds, otherwise the eroded surface will recover quickly. Usually, the resin liquid with trichloroethylene as the solvent is used as the source of solvent vapor. This method is often used for polyolefin plastics with complex shapes. In practical work, the following solvents are also commonly used to treat the surface of plastics. Others use chloroform or dichloromethane solvent, or a mixed solvent of toluene and acetone to treat the plastic surface, remove surface dirt and other objects, and clean the surface. The two mixed solvents can dry quickly and increase the fastness of printing and coating on the plastic surface.
Flame Treatment
The flame treatment method is to heat the air to a high temperature (above 3000 ℃) to form a plasma, which cleans and activates the surface of the material. The flame activates the oxygen molecules in the air, causing them to form polar molecules with carbon molecules on the surface of the material. The increase and oxidation of the surface molecular polarity reduces the surface tension of the plastic and increases the adsorption force of the material matrix to the ink.
Flame treatment used to be the most popular method for treating polyethylene, polypropylene and any plastic with a surface thickness of more than 10mm. But today, flame treatment remains only as part of the moulding or blow moulding process, in addition to the surface treatment of paper plates and materials for packaging food and beverages.
Corona Treatment
Corona treatment is to apply a positive voltage to the needle electrode opposite the flat electrode. When the voltage rises to a certain value, the light-emitting part extending from the needle tip will touch the flat electrode and be divided into many linear light-emitting parts. All are in a non-stop flashing state, and these light-emitting parts are plasma, which have the effect of cleaning and activating the surface of the material. The corona plasma produces free radical reaction on the plastic surface to cross-link the polymer, roughen the surface and increase its wetting of polar solvents. These plasmas enter the surface of the printed body by electric shock and penetration to destroy its molecules. structure, which in turn oxidizes and polarizes the treated surface molecules, activates the surface, and increases the adhesion of the substrate surface. Today, almost all plastic film, paper and metal foil materials are corona treated.
Plasma Treatment
Plasma is a substance in high vacuum conditions or under the action of strong electric field, high temperature, laser, neutral atoms or molecules will lose electrons, ionized into ions, such ions contain equal positive and negative charges, so it is called plasma. The principle of the treatment is: the radio frequency generator emits excitation energy at a higher voltage to produce a characteristic glow discharge phenomenon, so that the passing gas substance produces many excited electrons, ions and atoms, which then bombard the plastic surface, making the plastic surface The chemical groups change or form new groups or free radicals, resulting in deposition, achieving the purpose of chemical modification and physical modification of the polymer surface, resulting in polarity, which will interact with the polar groups in the ink binder. Butt, so that the ink adhesion is enhanced.
Anti-static Treatment
Because the plastic film has good insulation, the resistance is very large, and it is easy to carry static electricity and is difficult to remove. It is necessary to destaticize the plastic before printing to eliminate static electricity, remove dust and foreign matter, and avoid mesh blockage. The method of removing static electricity is mainly to remove static electricity with a static removing agent:
①Silicon-based antistatic agent, first use alcohols such as methanol or ethanol to remove grease and water; then use a brush or roller to repeatedly coat the antistatic agent or immerse the plastic film in the antistatic agent, at 30~40 ℃ Temperature and 60 ~ 80 ℃ temperature for 3 hours, after coating and drying, after drying for 5 hours before printing.
② Surfactant in addition to static agent. The principle of this method of removing static electricity is different from that of silicon-based static-removing agents. It is mainly achieved by increasing electrical conductivity and reducing surface resistance. The method can also be treated by roller coating method and dipping method.
-
Surface treatment of glass
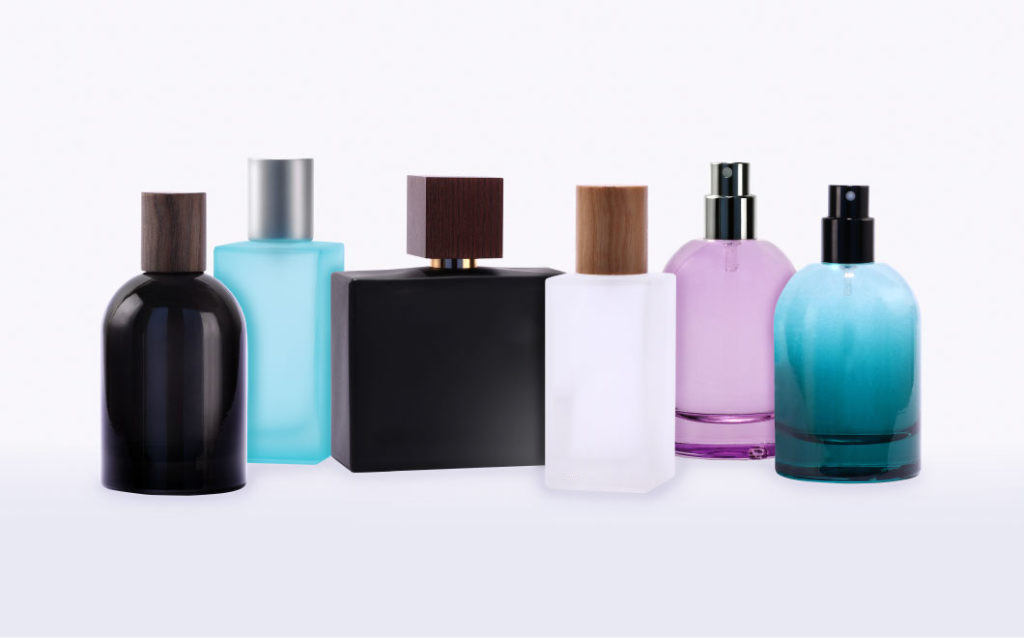
The main component of glass is SiO₂, and Si is mainly in the interior of the glass. The oxygen atoms are on the surface of the glass. This structure has a high surface energy, and it is easy to interact with other substances. If it encounters air, it will combine with the hydrogen in the air to form a hydrophilic structure. Gene, the hydrophilic group of OH (hydroxyl) floats on the glass surface, and it is difficult to attach the ink. There are alkali ions on the glass surface, forming Na-0 bonds. Such bonds are easily broken in air and water, making it difficult for ink to adhere. Therefore, it is necessary to treat the glass surface before printing. The methods of glass surface treatment are as follows:
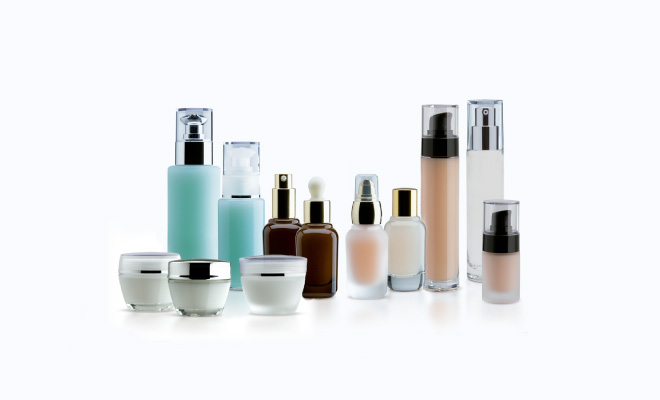
① Carry out liposensitive treatment. The liposensitive treatment is to coat various siloxane coupling agents on the glass surface to form liposensitive groups and improve the affinity of the glass to the ink.
②Degreasing treatment, remove grease to improve wettability, wash and degrease with acetone, methyl ethyl ketone, or degrease with dichloroethylene vapor.
③Strong acid treatment, through strong acid treatment, the alkali ions are removed to improve the ink adhesion.
④Physical treatment, light sandblasting with fine powder abrasives or water grinding with water abrasive paper can remove the attachments on the surface and improve the ink affinity.